Enhanced Corrosion Resistance: Aluminum is a reactive metal that readily reacts with oxygen in the air, forming an oxide layer. Although aluminum has some inherent resistance to oxidation, untreated aluminum parts are susceptible to oxidation and corrosion, especially in harsh environments. Surface treatment forms a protective oxide layer, effectively preventing further oxidation and corrosion, thereby extending the lifespan of the parts.
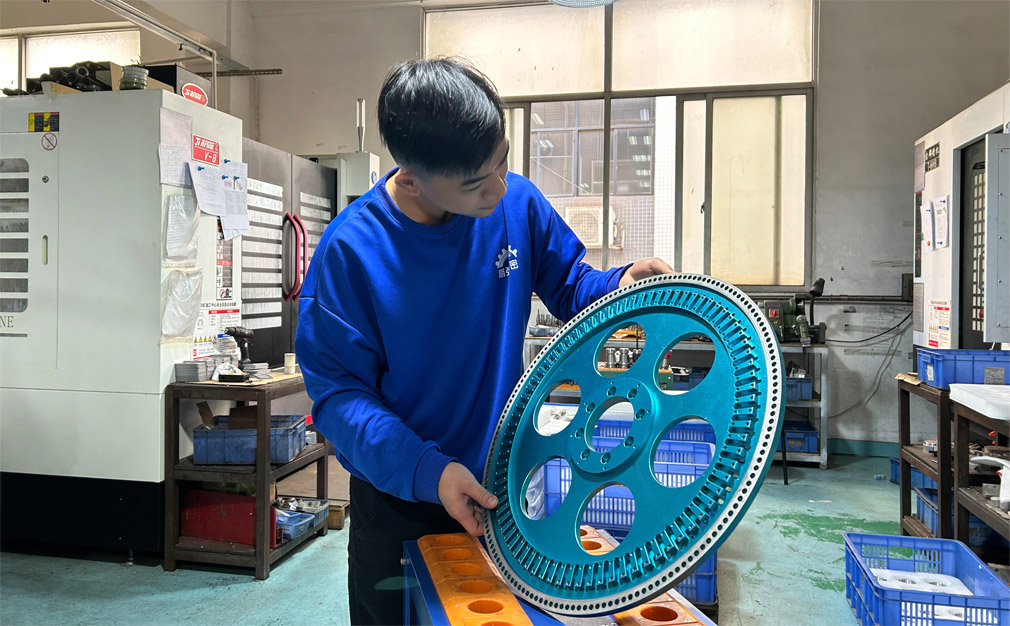
Improved Appearance: Surface treatment enhances the aesthetic appeal of aluminum machined parts, making them more visually appealing and uniform. Methods such as painting, anodizing, or electroplating can provide various colors and finishes, meeting customer demands for personalized appearance and enhancing the product's market competitiveness.
Enhanced Mechanical Properties: Proper surface treatment can improve the mechanical properties of aluminum parts, including hardness, wear resistance, and fatigue resistance. For example, anodizing forms a hard, wear-resistant oxide layer, increasing surface hardness and wear resistance, thus extending the part's lifespan. Coatings can also increase hardness and corrosion resistance, improving stability and reliability in harsh environments.
Improved Lubrication Properties: Surface treatment can improve the lubrication properties of aluminum parts, reducing friction and wear, thereby enhancing operational efficiency and performance stability. Coating with lubricating oil or coatings can reduce the friction coefficient of the aluminum surface, decreasing mechanical wear and energy consumption, and improving operational efficiency and energy savings.
Common Surface Treatments for Aluminum:
Anodizing: Anodizing is a common surface treatment method for aluminum, forming a dense and uniform oxide layer through anodizing in strong acid or alkaline solutions. This oxide layer provides excellent corrosion resistance and wear resistance and can be colored to achieve various aesthetic effects, suitable for both engineering and decorative purposes.
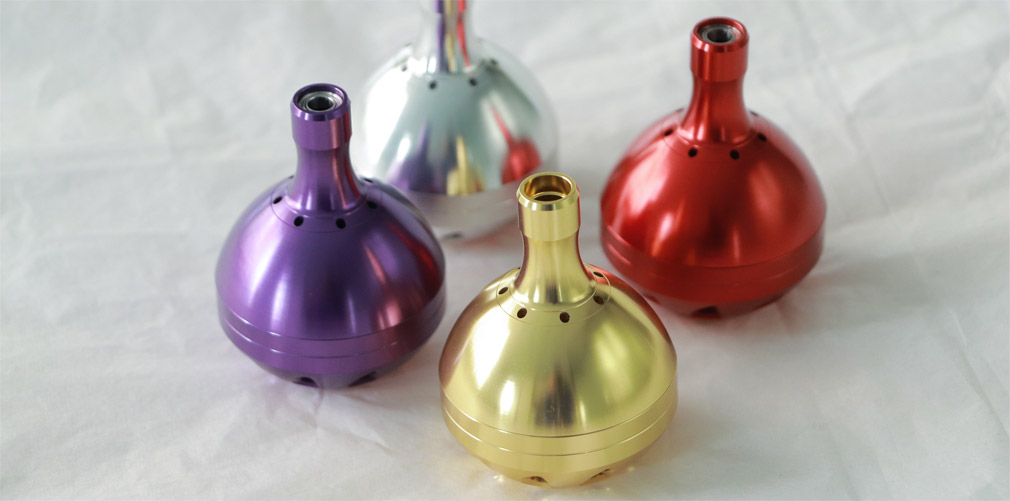
Coatings: Coating is a simple and effective surface treatment method where protective coatings are applied to aluminum surfaces, improving corrosion resistance and wear resistance. Common coating materials include paints, powder coatings, and polymer coatings, offering a wide range of options in terms of color and finish.
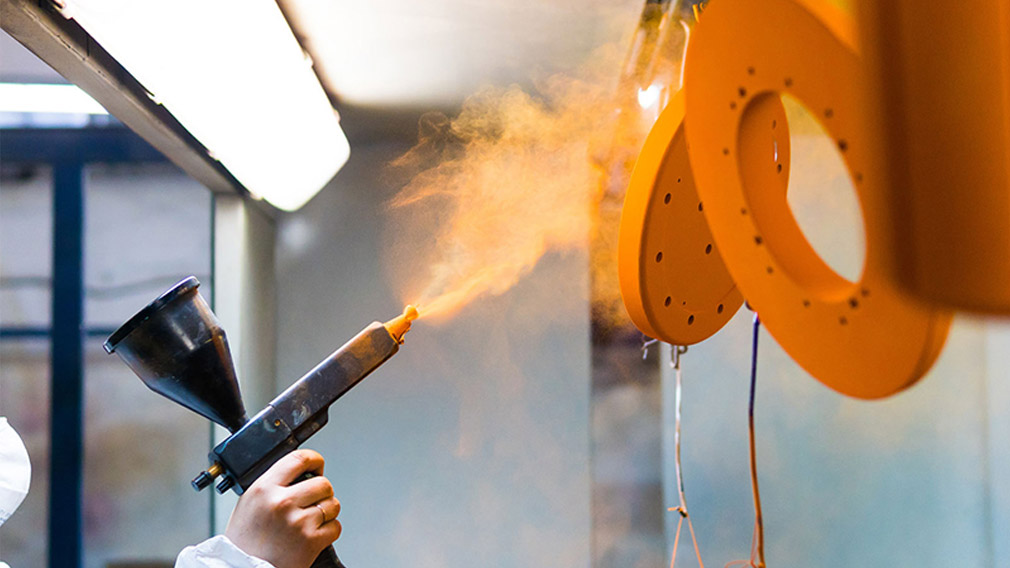
Electroplating: Electroplating involves depositing metal or alloy layers onto aluminum surfaces to improve their performance and appearance. Common plating materials include nickel, chromium, zinc, etc., which can increase hardness, corrosion resistance, and surface gloss, widely used in automotive, electronics, furniture, and other industries.
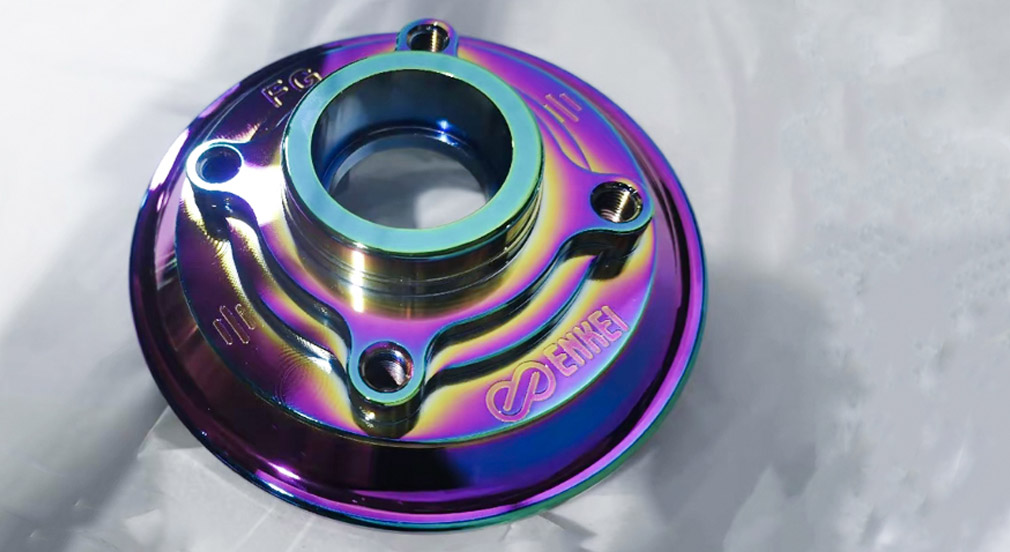
Mechanical Polishing: Mechanical polishing improves the smoothness and glossiness of aluminum surfaces through mechanical grinding and polishing processes. By selecting appropriate polishing techniques and materials, a mirror-like surface finish can be achieved, enhancing the appearance quality and decorative effects of aluminum parts.
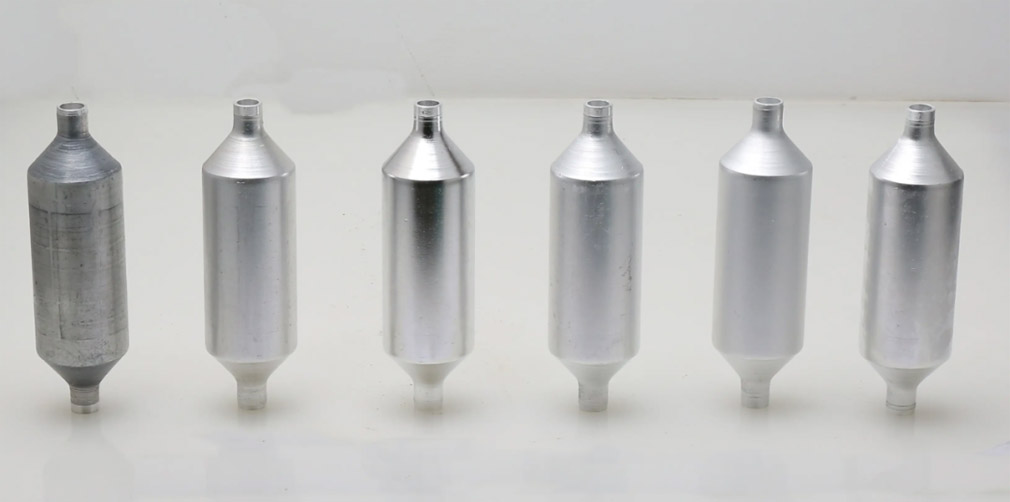
Chemical Treatment: Chemical treatment involves treating aluminum surfaces with chemical solutions to improve their surface properties and appearance. Common chemical treatments include acid etching, alkali washing, acid-base etching, etc., which remove oxide layers and impurities, improving surface quality and lubrication properties.
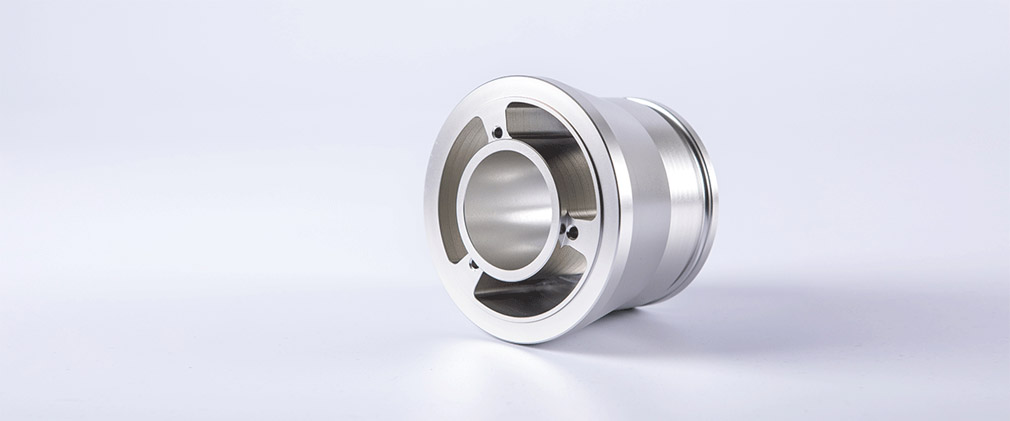
In conclusion, aluminum machined parts often require proper surface treatment to enhance corrosion resistance, improve appearance, enhance mechanical properties, and lubrication properties. Different surface treatment methods are applicable to different applications and requirements. Clients can choose suitable surface treatment solutions based on specific needs and budgets to ensure that aluminum parts have excellent performance and reliability. As a professional CNC factory, MQJM is committed to providing clients with professional surface treatment advice and services to achieve high-quality and personalized customization of aluminum machined parts.