Differences Between Sandblasting Anodizing and Direct Anodizing for Aluminum CNC Machined Parts
There are several key differences between sandblasting anodizing and direct anodizing for aluminum CNC machining parts. These differences primarily involve appearance, performance, and applications.
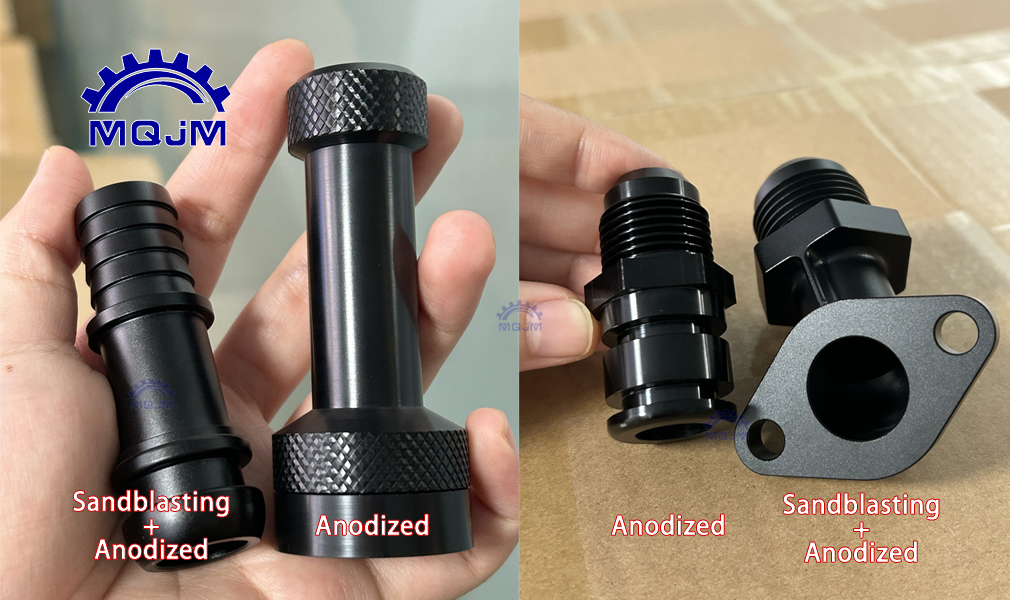
Sandblasting Anodizing
Process Steps:
1.Sandblasting: High-pressure abrasive blasting (e.g., aluminum oxide, glass beads) is used to treat the surface of aluminum CNC machined parts, removing impurities and irregularities, and creating a certain level of roughness.
2.Anodizing: The aluminum CNC machined parts are then subjected to an electrochemical process in an electrolyte solution, producing an aluminum oxide layer on the surface.
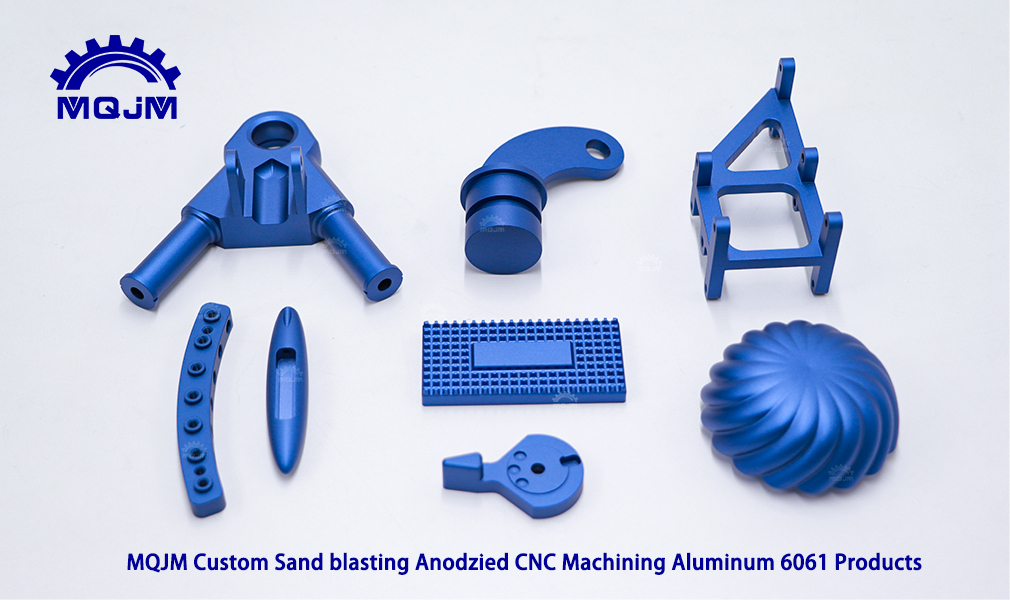
Characteristics:
1.Appearance: The sandblasted surface has a uniform matte finish, providing a better texture and a more refined feel.
2.Adhesion: Increased surface roughness from sandblasting improves the adhesion of the anodized layer to the substrate, resulting in a more uniform oxide film.
3.Wear Resistance: The anodized layer adheres more strongly, enhancing wear resistance.
4.Applications: Suitable for parts with higher aesthetic and performance requirements, such as high-end consumer electronics housings and aerospace components.
Direct Anodizing
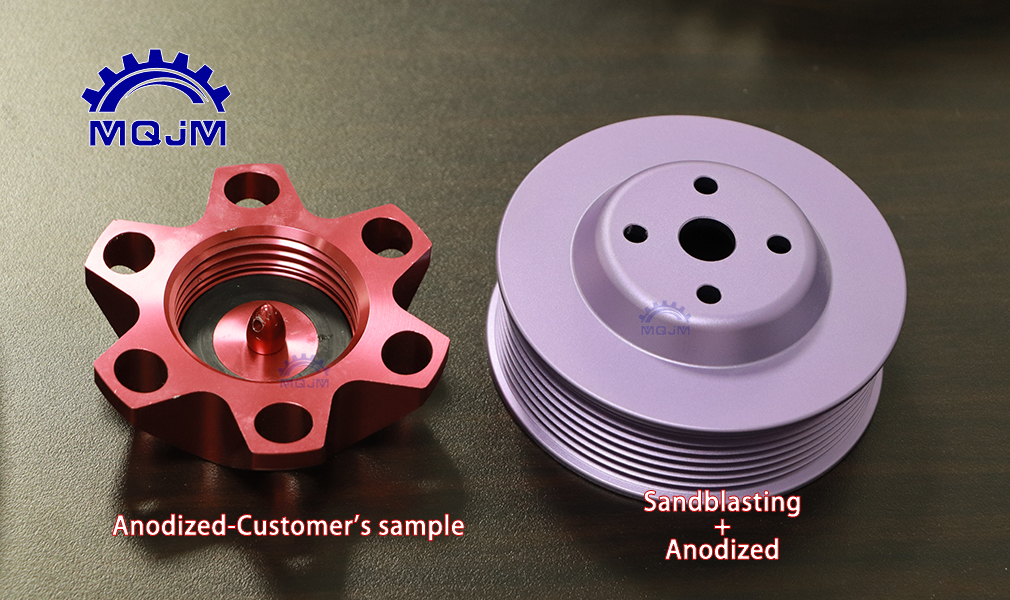
Process Steps:
1.Cleaning: Aluminum CNC machined parts are cleaned to remove oils, impurities, etc.
2.Anodizing: The cleaned parts undergo an electrochemical process in an electrolyte solution, forming an aluminum oxide layer on the surface.
Characteristics:
1.Appearance: Direct anodizing results in a surface with higher gloss and natural metallic sheen, but surface smoothness and uniformity might not match sandblasted surfaces.
2.Adhesion: Without sandblasting, the surface is relatively smooth, potentially leading to slightly lower adhesion of the oxide layer.
3.Wear Resistance: Good wear resistance, but may be slightly inferior to sandblasted anodizing.
4.Applications: Suitable for general industrial applications, architectural decorations, and cost-effective consumer products.
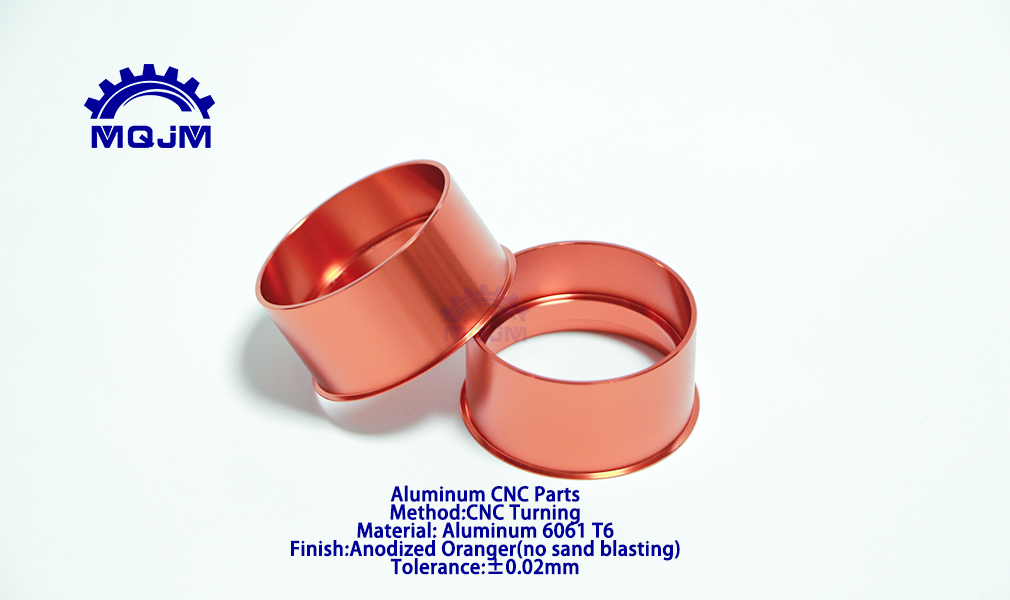
Which Treatment is Better?
The choice depends on specific application requirements:
1.Appearance Requirements: For a matte finish and refined texture, choose sandblasting anodizing.
2.Wear Resistance and Adhesion: Sandblasting anodizing typically performs better in these aspects.
3.Cost: Direct anodizing is simpler and more cost-effective.
In summary, if high demands are placed on the appearance and performance of aluminum CNC machined parts, sandblasting anodizing is the better choice. For general protective anodizing, direct anodizing may be more economical.