In the world of metal working and precision engineering, 6061 aluminum stands out as a versatile and highly sought-after material. Today, we begin to explore the precision machining process of 6061 aluminum.
6061 aluminum is known for its light weight, corrosion resistance and machinability. It is widely used in various industries, including aerospace, automotive, electronics, etc. However, to achieve precision machining of this alloy requires a combination of the right technology, tools and expertise.
A key aspect of machining 6061 aluminum alloy is choosing the right tool. Commonly used are high-speed steel and carbide cutting tools, each has its own advantages. For example, cemented carbide tools have higher hardness and durability, which can achieve higher turning speeds and longer tool life. However, they can be more expensive. High-speed steel tools, on the other hand, are cost-effective and suitable for less demanding applications.
The parameters of CNC turning and milling play a crucial role in achieving accuracy. According to the specific characteristics and processing operations of 6061 aluminum alloy, the cutting speed, feed speed and milling depth should be carefully optimized. Too high a turning speed can lead to excessive tool wear and poor surface finish, while too low a speed can lead to inefficient processing and extended production time. Again, feed speed and milling depth need to be adjusted to ensure smooth turning and minimal flutter.
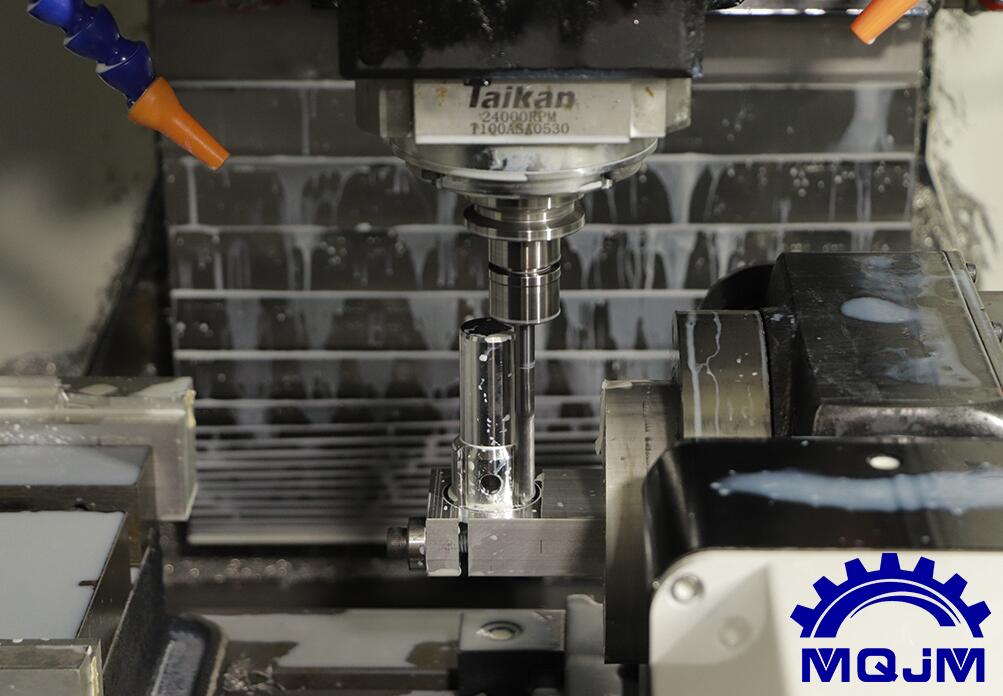
Another important consideration is the use of coolant. The coolant helps to reduce the heat generated during processing, which can affect the dimensional accuracy and surface finish of the workpiece. It also helps to extend tool life by reducing friction and wear. According to the specific requirements of the processing process, different types of coolants can be selected, such as water-based coolants and oil-based coolants.
Precision machining of 6061 aluminum uses advanced technologies such as CNC machining to provide greater accuracy, repeatability and flexibility, allowing complex geometry and tight tolerances to be easily achieved.
Surface treatment is also an important aspect of machining 6061 aluminum. Various surface treatment techniques, such as polishing, anodizing and powder coating, can be applied to improve the appearance and corrosion resistance of the parts. These technologies can also improve surface hardness and wear resistance, making parts more durable.
To sum up, machining 6061 aluminum requires a comprehensive understanding of the properties of the material, the selection of appropriate tools and CNC turning milling parameters, the use of coolants, and the application of advanced processing technologies. By paying attention to these factors, manufacturers can achieve a high level of precision and quality in 6061 aluminum parts that meet the demanding requirements of a variety of industries. Therefore, if you are involved in metal working or precision engineering, don't overlook the potential of 6061 aluminum and its precision machining capabilities.